.png?width=300&name=Webpage%20Headers%20(7).png)
Advantages of Powder Metallurgy
Powder Metallurgy, often abbreviated as PM, is a sophisticated manufacturing process used to create precise metal parts. The process encompasses several key steps: selecting the appropriate materials, compacting them into a desired shape, sintering to bond the particles, and, if necessary, performing additional operations such as steam treating, machining, lapping, or grinding.
One of the main advantages of PM is its cost-effectiveness in producing parts that are either simple or complex, with dimensions that are very close to the final specifications. The weight of these parts can range from as light as 0.68 grams (0.0015 lbs.) to as heavy as 6800 grams (15 lbs.).
Each part produced through PM requires a unique set of tooling, making this process particularly well-suited for moderate to high production volumes. This can translate to the production of several hundred to several thousand parts per hour.
Originally, PM was utilized for creating basic shapes such as bushings and bearings. However, advancements in the process now allow for the production of intricate, multilevel components.
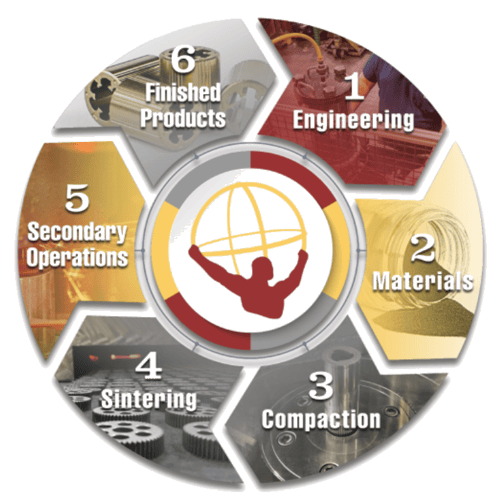
Advantages of PM Over Other Forming Processes
Powder Metallurgy (PM) stands out as a highly efficient and versatile manufacturing process, offering numerous benefits over traditional forming methods. Unlike other processes, PM allows for the production of complex and precise metal parts with minimal material waste. This method not only ensures cost-effectiveness but also enhances design flexibility, enabling the creation of intricate geometries that would be challenging or impossible to achieve with other techniques.
In this section, we will explore the key advantages of PM, including its ability to produce high-quality parts at competitive costs, its suitability for high-volume production, and its contribution to sustainable manufacturing practices. By understanding these benefits, you will gain insight into why PM is increasingly becoming the preferred choice for manufacturers across various industries.
.png?width=500&height=300&name=Website%20Images%20500%20X%20300%20(6).png)
Powder Metallurgy versus Casting
Casting is a process where molten metal is injected into a mold and allowed to harden to form the part. This method typically uses non-ferrous materials, primarily aluminum, magnesium, and zinc alloys.
Advantages of Powder Metallurgy Over Die Casting
Design Flexibility
- Casting: Limited by the need for draft angles, parting line considerations, and wall thickness.
- Powder Metallurgy: Allows for complex shapes and intricate features, with the added benefit of controlled porosity when needed.
Material Utilization
- Casting: Generates more waste due to the nature of the process.
- Powder Metallurgy: Provides superior material utilization with minimal waste, making it a more cost-effective and environmentally friendly option.
Tooling Costs
- Casting: Requires significant investment in dies and tools, which can be expensive.
- Powder Metallurgy: Tooling costs vary depending on part geometry, material, and size, often resulting in lower overall costs.
Both die casting and powder metallurgy are excellent for specific production volumes and part life. However, powder metallurgy stands out for its efficiency and flexibility in design and material usage.
Powder Metallurgy versus Machining
Machining is a general term that covers various processes to remove material from a solid metal blank to produce the desired part. Common machining processes include CNC turning, laser cutting, water jet cutting, and milling. The decision to use machining and the material selected depends on the part's complexity, dimensional and tolerance requirements, and the volume and timeframe needed for production. Materials used in machining include aluminum, brass, bronze, copper, carbon steel, stainless steel, tool steel, alloys, and sometimes plastics.
Machining is often used in combination with powder metallurgy, forging, die casting, and stamping as a secondary operation to achieve the final part specifications.
Advantages of Powder Metallurgy Over Machining
Design Flexibility and Material Utilization
- Machining: Involves removing material from a solid blank, which can result in significant waste.
- Powder Metallurgy: Allows for complex shapes and intricate details with minimal waste, providing better material utilization and cost efficiency.
Dimensional Accuracy and Surface Finish
- Machining: Typically offers superior dimensional accuracy, tighter tolerances, and improved surface finishes.
- Powder Metallurgy: While it may not always match the precision of machining, it excels in producing complex geometries at a lower cost.
Tooling and Lead Times
- Machining: Cutting tools can be expensive, and lead times are often long, especially for high-volume production.
- Powder Metallurgy: Tooling costs can vary, but the process generally supports faster production times and lower overall costs for complex parts.
Both machining and powder metallurgy have their strengths, but powder metallurgy stands out for its efficiency, flexibility in design, and better material utilization, making it a cost-effective alternative for many applications.
Powder Metallurgy versus Stamping
Stamping is the process of producing metal parts by pressing or punching metal sheets (or coiled metal) with a stamping press using a tool and die to form the part. Almost any type of metal or combination of metals can be used, with common materials including aluminum, stainless steel, carbon steels, and copper and brass. The selection of materials is determined by the application, formability, welding requirements, corrosion resistance, strength, and cost.
Advantages of Powder Metallurgy Over Stamping
Design Flexibility
- Stamping: Requires knowledge of how the metal will deform, including necessary radii, angles, and dimensional requirements.
- Powder Metallurgy: Allows for complex shapes and intricate features that are not typically achievable through stamping.
Material Utilization
- Stamping: Produces a considerable amount of excess material (scrap).
- Powder Metallurgy: Provides superior material utilization with minimal waste, making it a more cost-effective and environmentally friendly option.
Tooling and Setup Costs
- Stamping: Involves significant capital investment and high setup costs. Stamping dies are expensive and increase in cost with part complexity. The cost of stamping machines can also be high, further impacting overall production costs.
- Powder Metallurgy: Tooling costs can vary from very inexpensive to expensive, depending on part geometry, material, and size, often resulting in lower overall costs.
Both stamping and powder metallurgy are suitable for high-volume production. However, powder metallurgy stands out for its efficiency, flexibility in design, and better material utilization.
Powder Metallurgy versus Forging
.png?width=350&height=700&name=500%20X%201000%20Website%20Images%20(4).png)
Forging is the process of producing metal parts through mechanical deformation using compressive forces, shaping the part without removing or adding material. Almost any type of metal or combination of metals can be forged, with common materials including stainless steel, titanium, carbon steels, and other metal alloys. The selection of materials depends on the part's application requirements.
Advantages of Powder Metallurgy Over Forging
Design Flexibility
- Forging: Limited by the size of the press and the ability to produce simple shapes.
- Powder Metallurgy: Allows for complex shapes and intricate features, with the added benefit of controlled porosity when needed.
Material Utilization
- Forging: Typically requires machining to achieve the final shape, resulting in material waste.
- Powder Metallurgy: Provides superior material utilization with minimal waste, making it a more cost-effective and environmentally friendly option.
Tooling and Setup Costs
- Forging: Involves significant capital investment for the die and press. Additionally, labor, tooling, and material costs can be high.
- Powder Metallurgy: Tooling costs can vary from very inexpensive to expensive, depending on part geometry, material, and size, often resulting in lower overall costs.
Both forging and powder metallurgy are excellent for specific production volumes and part life. However, powder metallurgy stands out for its efficiency, flexibility in design, and better material utilization.
Powder Metal Design Specifications
At Atlas, our team of skilled engineers brings extensive industry experience and knowledge to guide you through every stage of your structural component requirements. From weight to shape, our flexibility is our expertise. We design and manufacture components with the following specifications:
- Weight: 453.59 grams (1 lb) to 1360.78 grams (3 lbs)
- Diameter: 0.32 cm (0.125”) to 12.7 cm (5”)
- Length: 0.635 cm (0.25”) to 3.81 cm (1.5”)
- Shapes: Structural, spherical, flanged
Our advanced molding, sintering, and sizing capabilities, combined with a robust quality metric system, enable us to handle parts of all sizes and complexities. Powdered metallurgy, an economical and eco-friendly manufacturing option, minimizes material waste and reduces costs.
.png?width=500&height=300&name=Website%20Images%20500%20X%20300%20(4).png)
Need a Solution?
Ask Us a Question
Contact Information
Mailing Address
125 Tom Mix Dr.
P.O. Box P
DuBois, PA 15801
USA
Phone
Fax
Testimonial
"Our Engineering team works directly with Atlas Pressed Metals to achieve our company goals. Atlas is always very helpful, gives us on-time delivery and the sales reps are always willing to research to get answers for our needs.”
- Amanda S., Associate Buyer | Healthcare Industry