.png?width=300&name=Website%20Industry%20Headers%20(4).png)
High-Precision Metal Parts Through Powder Metallurgy
Unlock new possibilities in metal part manufacturing with powder metallurgy. When off-the-shelf or machined components fall short, precision metal parts made through powder metallurgy offer an innovative path forward. This advanced process helps enhance part properties, improve design features, and reduce material waste and other costs — all without compromising performance.
Whether the goal is to simplify complex geometries, improve efficiency, or gain consistency at scale, powder metal components can be manufactured to your exact requirements. As a trusted parts supplier for nearly 50 years, Atlas Pressed Metals makes it easier to solve design and production challenges with durable, high-performance powder metal parts.
PM Solutions
Structural Parts
Built for strength, speed, and savings — high-precision, multilevel metal parts from Atlas deliver performance where it counts. Customers benefit from state-of-the-art engineering and metallurgy, extensive press and furnace options, and in-house secondary operations for reliable quality and shorter lead times.
.png?width=392&height=235&name=Website%20Images%20500%20X%20300%20(1).png)
Gears
Complex designs. Tight tolerances. Consistent performance. With advanced automation and in-house metallurgists, Atlas produces multilevel sintered metal parts like gears that reduce or eliminate secondary machining — saving time and cost.
Learn More →Bearings
Want to improve durability and reduce maintenance? Powder metal bearings and bushings are self-lubricating by design, cutting maintenance and extending lifespan — ideal for applications in:
- Automotive
- Consumer Goods
- Industrial Needs
Conversions
Switching to powder metal components can drastically lower material waste and post-processing needs. If you're ready for more efficient, cost-effective production, powder metal part conversions may offer advantages over forging, stamping, or machining.
Diverse Industries
Looking for a smarter way to manufacture? Whether you’re aiming to reduce assembly costs, boost part performance, or simplify production, Atlas works alongside you to design custom powder metal parts that meet your exact requirements. You’ll have access to advanced engineering, in-house secondary machining, and a full-service tool and die facility — all built to deliver high-precision metal components that perform under pressure.
Why Manufacturers Choose Powder Metal
- Smart, scalable solutions for complex, high-performance parts
- Reliable quality for both low- and high-volume production
- Flexible designs — from simple shapes to advanced structural components
- Broad material options, including heat-treatable blends for extra strength
- Built-in porosity for self-lubricating or filtration functions
- Tight dimensional tolerances for intricate geometries
- Net-shaping capabilities to reduce secondary machining
- Conversion of multi-part assemblies into one component, saving time, SKUs, and money
PM Solutions Design Gallery
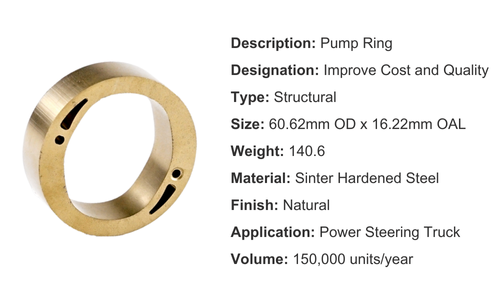
Powder Metal Design Specifications
Get exactly what your design demands — with the right size, shape, and strength for your structural components. Atlas’s experienced engineers collaborate with you at every stage to streamline design, reduce waste, and keep costs in check. From part complexity to material selection, flexibility is built into every custom metal part we create.
- Weight: 453.59 grams (1 lb) to 1360.78 grams (3 lbs)
- Diameter: 0.32 cm (0.125”) to 12.7 cm (5”)
- Length: 0.635 cm (0.25”) to 3.81 cm (1.5”)
- Shapes: Structural, spherical, flanged
Advanced molding, sintering, and sizing technologies make it easy to produce powder metal components of all shapes and complexities. This eco-friendly, cost-effective manufacturing method lowers scrap rates while delivering consistent, high-quality results.
.png?width=500&height=300&name=Website%20Images%20500%20X%20300%20(4).png)
Need a Solution?
Ask Us a Question
Contact Information
Mailing Address
125 Tom Mix Dr.
P.O. Box P
DuBois, PA 15801
USA
Phone
Fax
Testimonial
"Our Engineering team works directly with Atlas Pressed Metals to achieve our company goals. Atlas is always very helpful, gives us on-time delivery and the sales reps are always willing to research to get answers for our needs.”
- Amanda S., Associate Buyer | Healthcare Industry