.png?width=300&name=Webpage%20Headers%20(8).png)
Powder Metal Density Considerations
Powdered metal (PM) components offer an excellent, cost-effective alternative to machining metal components from wrought steel. One key difference between wrought steel and powder metal is density. The typical density range for the PM process varies depending on the application:
- Structural applications: 85% to 93% (6.6 g/cm³ to 7.3 g/cm³)
- Bearing applications: 75% to 87% (5.8 g/cm³ to 6.8 g/cm³)
In contrast, typical wrought steel material has a density of 100% (7.8 g/cm³).
With the PM process, other aspects such as density and chemistry can be adjusted, allowing for tailored part characteristics and performance. By choosing the appropriate density for an application, customers can trade the cost of a fully dense steel component for a more economical PM component.
.png?width=400&height=400&name=Website%20Images%20500%20X%20500%20(55).png)
Raw Material
At Atlas Pressed Metals, we work closely with our customers to understand the component’s application and requirements. Through our cooperative approach in material selection, we strive to provide cost-effective material solutions that meet all performance requirements.
Let’s explore a few different powder mixes and discuss the impact of powder selection on density:
- Copper alloyed steels (FC): These mixes contain small amounts of copper and often include graphite, resulting in a strong material at a reasonable price. The iron-copper family of alloys can achieve densities up to 90% (7.0 g/cm³) with conventional press and sinter processing.
- Iron Nickel (FN), Diffusion alloyed (FD), and Pre-alloyed (FL) materials: These materials can be pressed to densities over 90% (7.0 g/cm³) and up to 93% (7.3 g/cm³) using conventional pressing methods.
Selecting a material that aligns with the application’s needs is a crucial first step.
Compaction
The compaction process is the initial step in creating a powdered metal (PM) component. During compaction, the raw material, which is a fine particulate metal powder, is fed into a tool cavity and pressed into a near-finished geometry. Since the density of the compacted part is higher than the density of the powder, the powder will occupy a volume approximately twice that of the compacted part.
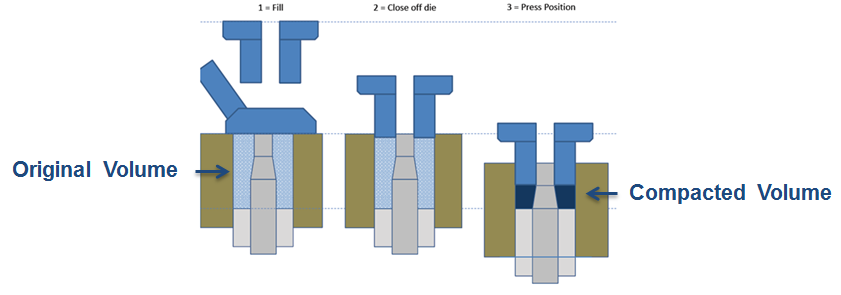
Sintering
After a part is compacted, the next operation is typically sintering. During the sintering process, powder particles bond to one another. The particles do not actually reach their melting temperature during sintering; instead, they form 'necks' with each other at elevated temperatures, as depicted to the right.

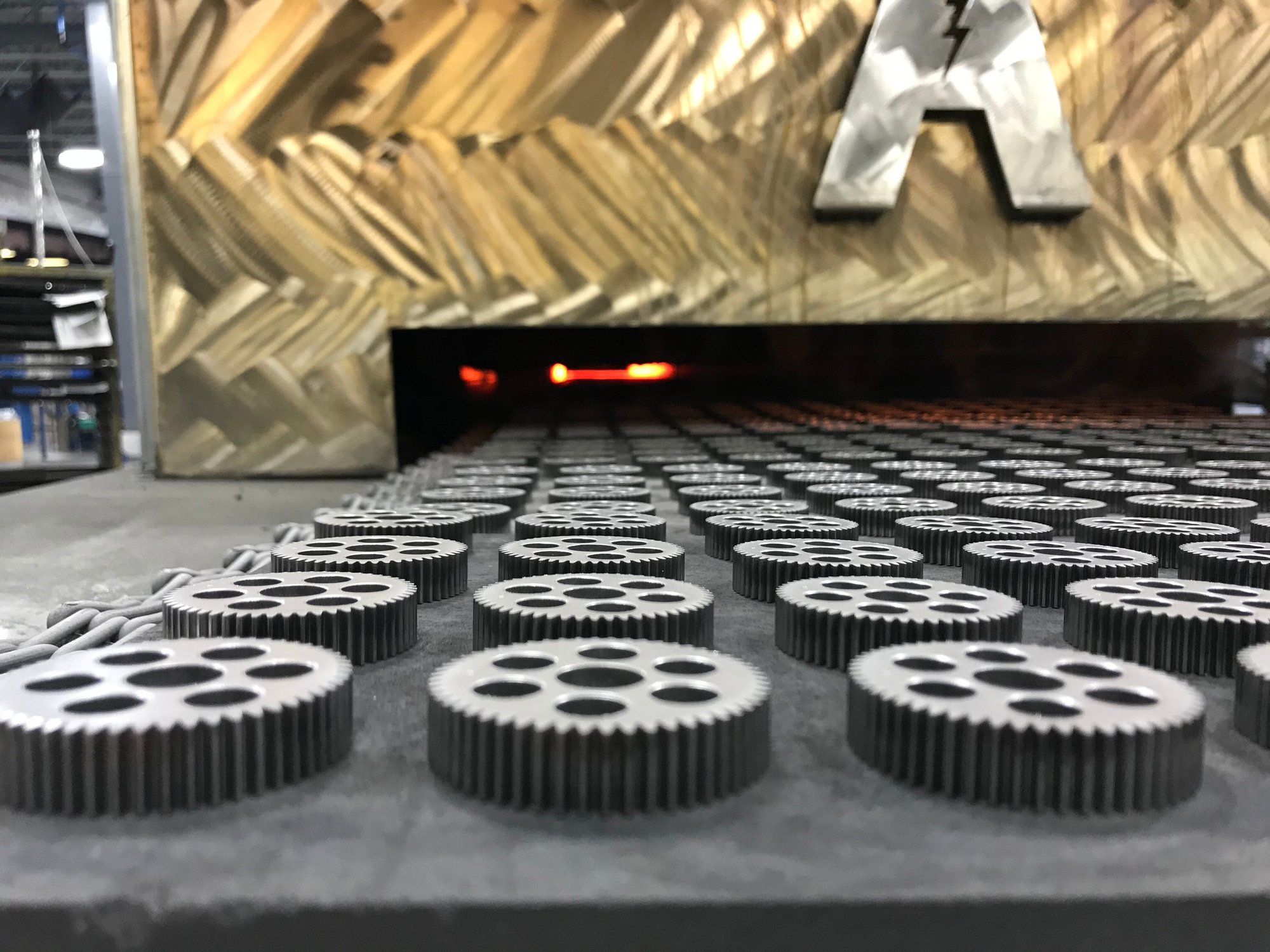
The effectiveness of particle bonding during sintering depends on the temperature and the duration at that temperature. Higher temperatures and longer sintering times result in better particle bonds.
A conventional sintering furnace can reach up to 1150°C (2100°F). The properties of most materials listed in standards like MPIF, ASTM, DIN, JIS, and SAE are based on conventional sintering temperatures of 1120°C (2050°F) for iron-based materials and approximately 815°C (1500°F) for copper-based materials. There are opportunities to improve densities during the sintering operation by increasing temperatures to 1260°C (2300°F) or beyond. As the part is heated, its size and porosity are reduced. At Atlas Pressed Metals, we have observed up to an 8% increase in density, meaning a 90% (7.0 g/cm³) molded density can increase to 97% (7.55 g/cm³), as shown in the above image. Achieving such temperatures requires a high-temperature sintering furnace, which impacts the cost of manufacturing a component since sintering is often the most expensive part of the PM manufacturing process.
Infiltration While Sintering
Copper infiltration is another method to increase density in PM components. Although this process is being replaced by some technological advancements, it is still used to enhance density and mechanical performance.
Copper infiltration can achieve densities up to 93% (7.3 g/cm³) and improve strength. In this process, a predetermined amount of copper is assembled onto a compacted component before sintering. During the sintering operation, the copper melts and infiltrates the component. However, the popularity of this process is declining due to the cost of copper and the required assembly. Similar results can now be achieved with modern powder alloys and compaction techniques.
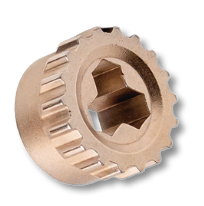
Sizing
A secondary operation called sizing or restriking is an optional process that may be employed after sintering to increase density, among other benefits. Sizing is not commonly used solely to increase density; it is more frequently utilized for post-sinter dimensional control, with increased density being a secondary advantage of the sizing process.
Need a Solution?
Ask Us A Question
CONTACT INFORMATION
Mailing Address
125 Tom Mix Dr.
P.O. Box P
DuBois, PA 15801
USA
Phone
Fax
TESTIMONIALS
Atlas Pressed Metals has been a long time supplier to our company. They are reliable, responsive to quotes, and always have met our deadlines.
Their communication is thorough and we have been most happy with our sales representative. We feel strongly that we should treat our customers and suppliers as we would like to be treated, and Atlas seems similar in this regard. It is a pleasure to do business with them.”
- Bruce C., President | Appliance Industry
.png?width=500&height=500&name=iso-no-background-(1).png)
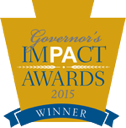
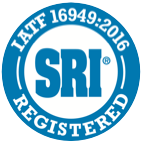