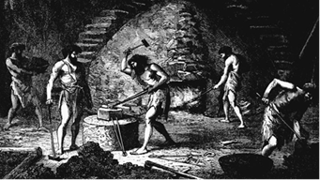
Improving on an Ancient Process, Modern Methods of Heat Treating Sintered Steel
Innovative Solution #11215
The use of Sinter Hardened Powder Metal to address the strength, cleanliness, and economic requirements of a small cylindrical housing with intricate features.
Overview
Precise tooling was developed to create fine detail on the component's exterior. On the interior, the core pin creates all of the interior veins. The tips of the veins that outline the interior pockets have the same thickness as five metal powder particles or 500microns. Since milling and electrical discharge machining (EDM) cannot be applied cost-effectively given the high production volume for this part, powder metal became the method of choice for the customer.
Challenge
Atlas Engineers were then tasked with selecting the appropriate material blend to control density variations with this challenging geometry and manufacturing strategy.
Results
A sinter hardened material was selected primarily to avoid the potential for distortion and variation thereby improving the overall tolerance of the component. Additionally, a proprietary lubricant was blended with the sinter hardened material further boosting the manufacturing performance by supporting part integrity throughout the compaction cycle and allowing for increase cycle time.
Interested in reading more about heat treatments options in the Powdered Metal process? Click here to read “Powder Metallurgical Solution for a Complex Geometry Coupler Requiring High Dimensional Stability and Microstructure Uniformity through Heat Treatment” written by Dr. Craig Stringer, Andy Wright ad Pete Imbrogno of Atlas Pressed Metals. Dr. Stringer presented this paper at ASM International Heat Treat 2021 Conference in St. Louis on September 14-16th, 2021.
ASM International is the world’s largest association of material-centric engineers and scientists. ASM is dedicated to informing, educating, and connecting the materials community to solve problems and stimulate innovation around the world.
Related Case Studies
Need a Solution?
Ask Us A Question
CONTACT INFORMATION
Mailing Address
125 Tom Mix Dr.
P.O. Box P
DuBois, PA 15801
USA
Phone
Fax
TESTIMONIALS
After finding Atlas Pressed Metal on the internet and a site visit by our CEO, we were impressed with the Atlas plant, the team and the product.
We used them for a powdered metal part for one of our customers and we have continued to use them for about 5 years. We are pleased with their expertise in making good suggestions and with their customer service.”
- John R., CNC Sales Manager | Machined Parts Manufacturer
.png?width=500&height=500&name=iso-no-background-(1).png)
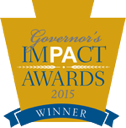
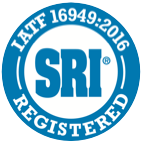