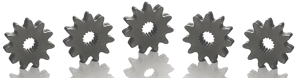
Manufacturing Engineering Consulting Services: Powder Metal Conversion
Looking to boost efficiency, reduce costs, and elevate part performance?
Traditional metal manufacturing methods—like casting, stamping, welding, and CNC machining—have served us well, but they often come with challenges:
- Higher production costs due to material waste and multi-step processes
- Extended lead times that delay market delivery
- Design constraints that limit innovation
- Inconsistent tolerances that require extra finishing and assembly work
At a certain point, even the best efforts in stamping cost reduction or machining optimization hit a wall. That’s where powder metallurgy comes in. If you're ready to push past these limitations, powder metallurgy offers a smarter, more streamlined alternative that unlocks cost savings, design flexibility, and consistent performance.
What is a Powder Metal Conversion? (And Why It Matters)
Powder metal conversion is an alternative to traditional manufacturing processes that redesigns parts with more cost-effective and optimized engineering.
Rather than machining away material or casting molten metal, powder metallurgy compacts and sinters fine metal powders into high-precision components. This method enables:
- Complex, intricate designs
- < 5% material waste and greater efficiency
- Stronger, more consistent parts with tight dimensional tolerances
- Significant cost savings — especially for medium-to-high-volume production
In the right application, powder metal conversion can completely transform how your part is designed and manufactured — enhancing performance, extending service life, and significantly improving profitability.
Benefits of Powder Metal Conversions
See how Atlas Pressed Metals helps companies like yours overcome manufacturing obstacles and improve outcomes:
- Appliance manufacturer:
Converted a washing machine lid cam to sinter-hardened powder metal — achieving a 66% cost reduction while doubling material strength to support a switch from metal to glass lids, all without requiring secondary machining or heat treatment. - Automotive supplier:
Designed and produced a highly complex gear as a single, net-shape part with tight tolerances and faster turnaround. Run-out specification is 0.00267 inch (0.068 mm) max, while the part’s overall length had to be held within ±0.00196 inch (0.05 mm), - Tool manufacturer:
Converted a complex part with intricate internal veins and external alignment features to sinter hardened powder metal — achieving precision, cost savings, and dimensional stability without secondary heat treatment.
If you’re facing high costs, complex designs, or performance limitations with your metal parts — conversion might be the solution you’ve been searching for.
Can Powder Metallurgy Solve Your Manufacturing Problems?
It depends on the situation. We begin with a manufacturing design consultation to get more information about your part. If your application is a match, PM conversion can replace costly machining and secondary treatments with a more efficient process. By compacting and sintering metal powders into near-net or net-shape parts, you gain immediate, measurable advantages:
- Simpler design & assembly:
Replace multi-piece assemblies with a single, strong powder metal part. - Lower cost per part:
Eliminate machining, secondary heat treatments, and scrap losses. - Freedom to innovate:
Produce complex geometries, high-precision internal structures, and fine features that are too expensive or impossible through traditional methods. - Consistent high-quality results:
Ensure tight dimensional tolerances and repeatability across low-to-high-volume production runs.
If you’re unsure whether powder metallurgy is the right fit, our mechanical engineering consulting services can help. We’ll evaluate your part, application, and production goals through a collaborative manufacturing design consultation to determine if powder metal conversion offers cost and performance advantages.
Use raw materials efficiently, minimize scrap, skip machining operations, and increase throughput.
Easily manufacture unique designs with enhanced durability, precise surface finishes, and fine edge details.
Maintain uniformity and precise tolerances across every part — delivering reliable quality at any scale.
Learn More About Powder Metallurgy Solutions
Explore how to overcome metal parts manufacturing challenges:
Watch Powder Metal Conversion in Action:
Company Workshops:
Need a Solution?
Ask Us a Question
Contact Information
Mailing Address
125 Tom Mix Dr.
P.O. Box P
DuBois, PA 15801
USA
Phone
Fax
Testimonial
"Our Engineering team works directly with Atlas Pressed Metals to achieve our company goals. Atlas is always very helpful, gives us on-time delivery and the sales reps are always willing to research to get answers for our needs.”
- Amanda S., Associate Buyer | Healthcare Industry