.png?width=300&name=Webpage%20Headers%20(19).png)
What is a Powder Metal Bearing?
A powder metal bearing is a type of bearing made from powdered metal that is compacted and sintered to form a solid piece. These bearings are known for their ability to evenly distribute lubrication across their working surface, which enhances their performance and longevity. They are used in various applications, including control systems and fractional horsepower motors, and can be made from materials like bronze and iron graphite blends. Additionally, they can be impregnated with oil to further increase their lifespan and efficiency.
.png?width=400&height=400&name=Website%20Images%20500%20X%20500%20(38).png)
Applications for Powder Metal Bearings
Automotive
- Windshield wipers
- Power window mechanisms
- Seat adjusters
- Motors
- Brakes
- Pumps
Consumer Goods
- Blenders
- Garbage disposals
- Washing machines
- Hand tools
- Toys
- Furnitures
Industrial
- Scientific equipment
- Computers
- Construction equipment
- Conveyers
Additional Benefits of Using PM for Bearings
Powder Materials for Bearings
Bronze Powder Bearings
Bronze powder is the most common choice for bearings due to its excellent wear resistance and self-lubricating properties. These materials feature 12-30% interconnecting porosity to contain lubricating oil. With a 10% addition of tin, bronze provides corrosion resistance, can manage shock loading, and offers the necessary ductility for staking. Graphite is often added to the mix for improved lubricity, with the percentage ranging from 1% to 3.5% depending on the component's specific application requirements.
Iron or Ferrous Alloy Bearings
Iron or ferrous alloys are harder and stronger than bronze powder. Various alloys in this category are designed to meet specific component and application requirements. These bearings are often referred to as “structural bearings.”
Material Selection Considerations
Balancing the requirement for high porosity for lubrication with other operating conditions such as load, temperature, sound, and speed is crucial in material selection.
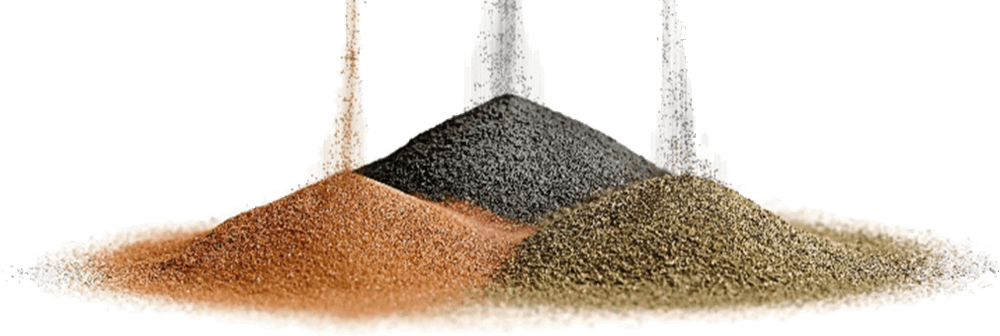
Powder Metal Process
.png?width=300&name=Website%20Images%20500%20X%20500%20(49).png)
Collaborative review of your new part design or an evaluation of a potential conversion to powder metal for an existing part
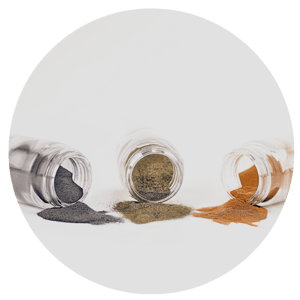
Selecting the best powder or powder blend for durability, reliability, and accuracy
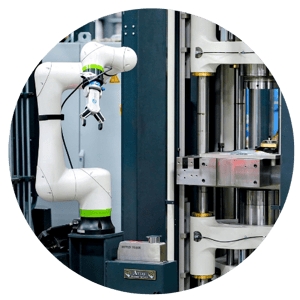
Compacting the metal powder to precise specifications under controlled pressure
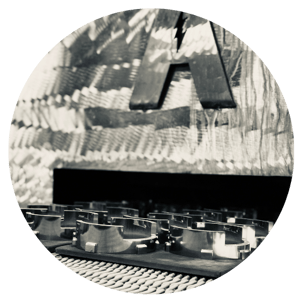
Heating or "Sintering" to create a permanent form
Powder Metal Design Specifications
At Atlas, our team of skilled engineers brings extensive industry experience and knowledge to guide you through every stage of your structural component requirements. From weight to shape, our flexibility is our expertise. We design and manufacture components with the following specifications:
- Weight: 453.59 grams (1 lb) to 1360.78 grams (3 lbs)
- Diameter: 0.32 cm (0.125”) to 12.7 cm (5”)
- Length: 0.635 cm (0.25”) to 3.81 cm (1.5”)
- Shapes: Structural, spherical, flanged
Our advanced molding, sintering, and sizing capabilities, combined with a robust quality metric system, enable us to handle parts of all sizes and complexities. Powdered metallurgy, an economical and eco-friendly manufacturing option, minimizes material waste and reduces costs.
.png?width=500&height=300&name=Website%20Images%20500%20X%20300%20(4).png)
Need a Solution?
Ask Us a Question
Contact Information
Mailing Address
125 Tom Mix Dr.
P.O. Box P
DuBois, PA 15801
USA
Phone
Fax
Testimonial
"Our Engineering team works directly with Atlas Pressed Metals to achieve our company goals. Atlas is always very helpful, gives us on-time delivery and the sales reps are always willing to research to get answers for our needs.”
- Amanda S., Associate Buyer | Healthcare Industry