.png?width=300&name=Webpage%20Headers%20(8).png)
Rules of Thumb for Manufacturing with Powder Metal
At Atlas Pressed Metals, we offer iron-copper and copper-steel materials designed for medium-strength structural applications. Our materials typically feature 2% copper content, providing an optimal balance of strength and performance.
For projects requiring secondary machining, our materials can be specified with combined carbon contents of less than 0.5%, ensuring precision. Additionally, these materials can be heat-treated to enhance strength and wear resistance.
For applications needing extra wear resistance or where heat treatment isn't practical, higher copper content materials are available. Lower density parts can also be oil impregnated for self-lubrication.
Straight Surfaces
When designing PM components, it's crucial to keep surfaces formed by the die and lower pressing actions as straight as possible. Unlike plastics or die castings, which often have draft angles, our process allows for straight, clean angles, providing an advantage that many customers may not realize is achievable.
Overall Length, Outside Diameter, and Wall Thickness
The following design rules are interconnected: overall length (OAL) in relation to outside diameter (OD) and wall thickness. It is essential to avoid features that are either too thin or excessively long, as these can hinder material flow and negatively impact the formation of the finished part. Our recommendations are as follows:
- When using multi-action tools, maintain a minimum wall thickness of 0.100 inches.
- For applications requiring high density, consider a wall thickness range of 0.125 to 0.200 inches.
Increasing the wall thickness helps control tool deflection, which is crucial due to the higher forces needed to achieve greater density. Here are some examples, demonstrating these rules:
Example 1

Maximum OAL to OD ratio of 3:1
Example 2
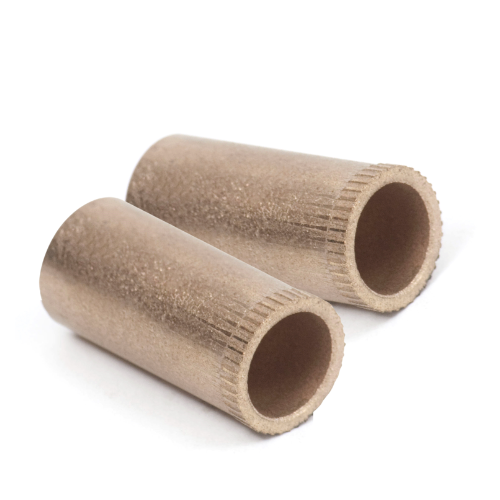
Maximum OAL to wall thickness ratio of 3:1
Example 3
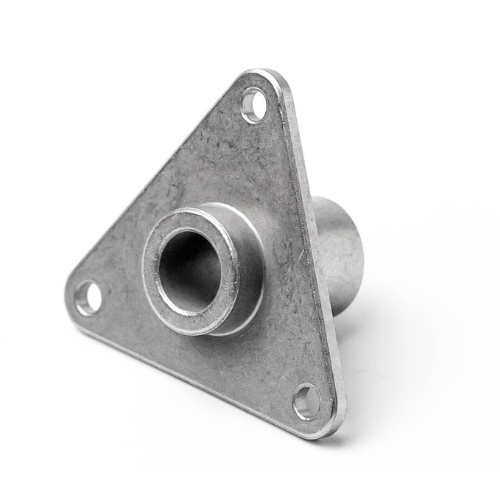
Minimum wall thickness between levels of 0.100"/2.55mm
Example 4
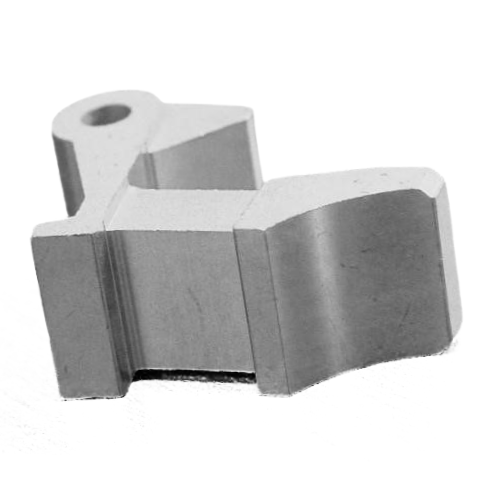
Level Pressed without Fill Adjustment
Parting Lines Between Tool Members
In other forming technologies, a deburring process is often used to remove flash formed during manufacturing. In PM, we use a chamfer to prevent a parting line from appearing on the working surface of the part. A small flat is designed into our tooling at the outer edge of the feature, strengthening the chamfer form and improving tool wear.
If transitions need to be smooth or used as a lead, we accommodate this in our tooling. This may require moving the parting line away from those transitions to another area of the part.
Surface Finish
The typical surface finish of a PM part is Ra 63µ"/1.6µm or better.
When dealing with areas intended as sliding or contact surfaces, such as the tooth of a gear, the sidewall features will often have a much better finish than Ra 63. This is because the ejection of the part from the tooling enhances the surface finish.
Need a Solution?
Ask Us a Question
Contact Information
Mailing Address
125 Tom Mix Dr.
P.O. Box P
DuBois, PA 15801
USA
Phone
Fax
Testimonial
"Our Engineering team works directly with Atlas Pressed Metals to achieve our company goals. Atlas is always very helpful, gives us on-time delivery and the sales reps are always willing to research to get answers for our needs.”
- Amanda S., Associate Buyer | Healthcare Industry