.png?width=300&name=Webpage%20Headers%20(17).png)
What is a Structural Powder Metal Component?
In powder metallurgy, a structural component is designed to carry and withstand mechanical loads and stresses within a larger structure or assembly. These components provide strength, rigidity, and support to the overall finished structure.
.png?width=300&height=300&name=Website%20Images%20500%20X%20500%20(4).png)
Key Benefits of Structural Powder Metal Components
- Strength and Durability: The strength of structural powder metal components comes from selecting the appropriate metal powder and optimizing compaction and sintering strategies. This results in improved tensile and yield strength, as well as hardness.
- Precision and Consistency: Powder metallurgy allows for tight tolerances, dimensional accuracy, and consistency, accommodating all production volume requirements.
- Cost-Effectiveness: High material utilization makes powdered metal a cost-effective choice. Producing components to tight tolerances often eliminates or reduces the need for additional operations, saving both time and costs.
- Eco-Friendly Process: Powdered metal is a green process with low energy usage and minimal scrap, making it more economical than standard machining, casting, or other metal-forming technologies.
Applications for Structural Components
Appliances
- Control Levers
- Hinge Components
- Bearings
- Cams
- Electric Motor
- Motor Cores
- Gears
- Stators
- Bearings
Automotive
- Cams
- Gears
- Pawls
- Inserts
- Pistons
- Valving
- Hinges
Industrial
- Cams
- Gears
- Rollers
- Plates
- Hinges
- Pump Rotors & Vanes
- Pump Rings
Tools
- Pawls
- Gears
- Simple & Structural Spacers
Additional Benefits of Using PM for Structural Parts
Powder Materials for Structural Applications
Iron Powder: The most commonly used material for structural applications. It can be used alone or combined with alloying materials like carbon, copper, nickel, and molybdenum to enhance mechanical properties.
- Carbon Steel: Made from a mixture of iron and graphite powders. During sintering, graphite is absorbed into the iron, producing a steel structure. Prealloyed carbon steel is also available for specific applications.
- Copper Steel: Produced by adding copper powder to iron powder, resulting in improved strength and hardness.
- Nickel Steel: Adding nickel (with or without copper) to iron powder creates high-strength components with favorable fatigue strength.
- Other Additives: Infiltration of lower melting materials like copper can increase density and impact resistance. Adding small amounts of phosphorus enhances electromagnetic properties, ductility, and strength.
Low Alloy Steels and Diffusion-Alloyed Steels: Made from prealloyed steel powders using nickel, molybdenum, and manganese. These are used when high performance and hardenability are required.
Electromagnetic Materials: Used when components require good permeability, purity, and density.
Stainless Steel Powder Metals: Required for applications needing significant mechanical properties and high corrosion resistance.
Copper Base Materials: Include pure copper, brass, bronze, and nickel silver. Each is selected for characteristics like electrical or thermal conductivity, oil impregnation, machinability, ductility, or corrosion resistance.
Aluminum Powders: Offer good corrosion resistance, excellent finishing properties, high strength-to-weight ratios, and vibration and sound-damping features.
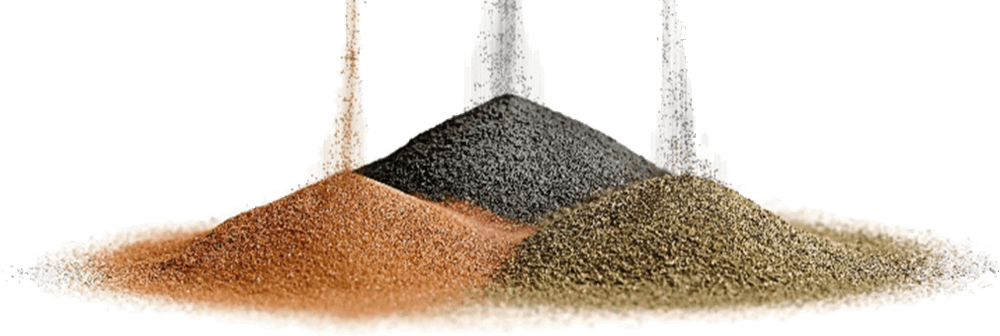
Powder Metallurgy Process
.png?width=300&name=Website%20Images%20500%20X%20500%20(49).png)
Collaborative review of your new part design or an evaluation of a potential conversion to powder metal for an existing part
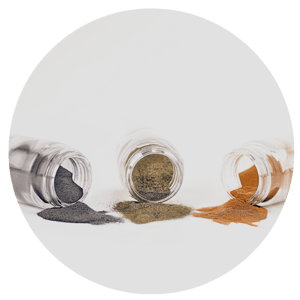
Selecting the best powder or powder blend for durability, reliability, and accuracy
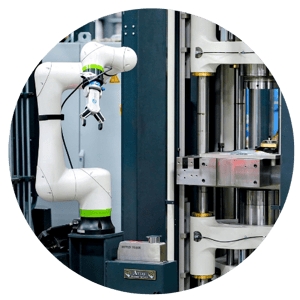
Compacting the metal powder to precise specifications under controlled pressure
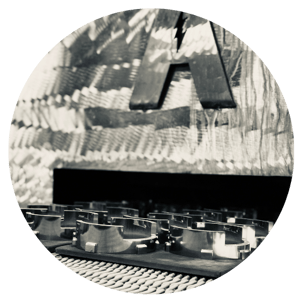
Heating or "Sintering" to create a permanent form
Powder Metal Design Specifications
At Atlas, our team of skilled engineers brings extensive industry experience and knowledge to guide you through every stage of your structural component requirements. From weight to shape, our flexibility is our expertise. We design and manufacture components with the following specifications:
- Weight: 453.59 grams (1 lb) to 1360.78 grams (3 lbs)
- Diameter: 0.32 cm (0.125”) to 12.7 cm (5”)
- Length: 0.635 cm (0.25”) to 3.81 cm (1.5”)
- Shapes: Structural, spherical, flanged
Our advanced molding, sintering, and sizing capabilities, combined with a robust quality metric system, enable us to handle parts of all sizes and complexities. Powdered metallurgy, an economical and eco-friendly manufacturing option, minimizes material waste and reduces costs.
.png?width=500&height=300&name=Website%20Images%20500%20X%20300%20(4).png)
Need a Solution?
Ask Us a Question
Contact Information
Mailing Address
125 Tom Mix Dr.
P.O. Box P
DuBois, PA 15801
USA
Phone
Fax
Testimonial
“We have found Atlas Pressed Metals to be a solid organization that has a genuine commitment to the success of their customers. They have provided us with a great quality product and excellent service.”
- A Satisfied Customer, Supply Chain Manager | Hardware Industry