A Leading Powder Metal Parts Manufacturer
Atlas Pressed Metals, a leading powdered metal parts manufacturer, is a family-owned business established in 1976. Our commitment to outstanding service is more than just a phrase—it's a fundamental aspect of our business. We take pride in our responsiveness to customers and continuously strive to enhance our service.
Mission:
To partner with customers and provide them with high quality design, engineering services, and engineered powder metal components for demanding and complex requirements.
Vision:
Atlas Pressed Metals is committed to a growth strategy that will enhance every aspect of our business. We will continue to earn the respect and opportunity from our customers through integrity, innovation, and a passion to provide world-class service.
Values:
We will treat all suppliers, customers, and personnel with the same fairness, respect, dignity, and concern that each of us would wish to be treated.
"As we work toward a better tomorrow, we do so with the intent of maintaining the same basic values the company was built upon. It is an extremely exciting time at Atlas, and I am optimistic about our future." - Jude Pfingstler, President
Atlas Organization
Atlas employs a team of engineering and metallurgical professionals who understand the intricacies of the powder metal process and materials. We provide powder metal engineering services on the front end in the form of product development, design assistance, and material selection.
Your dedicated Regional Sales Manager will provide access to the capability and capacity of Atlas’ organization (100+ employees).
Customer Commitment
At Atlas Pressed Metals, outstanding service is more than just a phrase—it's a crucial part of our business. We pride ourselves on our responsiveness and dedication to understanding and meeting our customers' needs. A commitment to reliable and consistent customer service is at the core of what we do. As our partner you will receive:
- Collaborative, Transparent Partnership
- Prompt and Honest Feedback
- Top-Notch Engineering Capabilities and Equipment
- In-House PM Solutions for Total Process Control
- Part Inventory for Quick Lead Times
- Smart Manufacturing Platform to Support Production
- Comprehensive Emergency Recovery & Backup Plan
- Commitment to Provide 100% On-Time Delivery
-1.png?width=1500&height=750&name=Untitled%20design%20(59)-1.png)
Our Culture
The Golden Rule is a way of life at Atlas Pressed Metals. We believe in treating others with respect and integrity, which is reflected in our positive work environment and strong customer relationships.
Employee Testimony:
“I really enjoy working at Atlas. I have worked here for over a decade. I like that fact it is a family-owned and -operated company. Everyone is really nice and supportive. It's nice to work with people that care about you and the job they are doing. "
- Christina Mahlon | Atlas Team Member Since 2006
Premier Powder Metal Solutions
Structural Parts
Atlas’s state-of-the-art metallurgical and engineering capabilities, combined with our wide variety of presses, sintering furnaces, and in-house secondary operations, offer our structural component customers the opportunity for high-quality components, reduced turnaround, and cost savings.
.png?width=392&height=235&name=Website%20Images%20500%20X%20300%20(1).png)
Gears
Our state-of-the-art automation and material handling systems and our in-house expert metallurgists allow Atlas to produce multilevel gears with internal configurations to tight tolerances to eliminate or reduce the need for additional operations.
Learn More →Bearings
Our company's first market was powder metal bearings. Custom metal bearings and bushings crafted through PM allows for the impregnation of parts with lubrication, which extends run-time and minimizes maintenance.
Conversions
Powder metal conversions are emerging as a game-changer, offering customers cost efficiency by reducing material waste and minimizing secondary operations. This makes it a more economical choice compared to traditional manufacturing methods.
Celebrating over 45 Years of Excellence
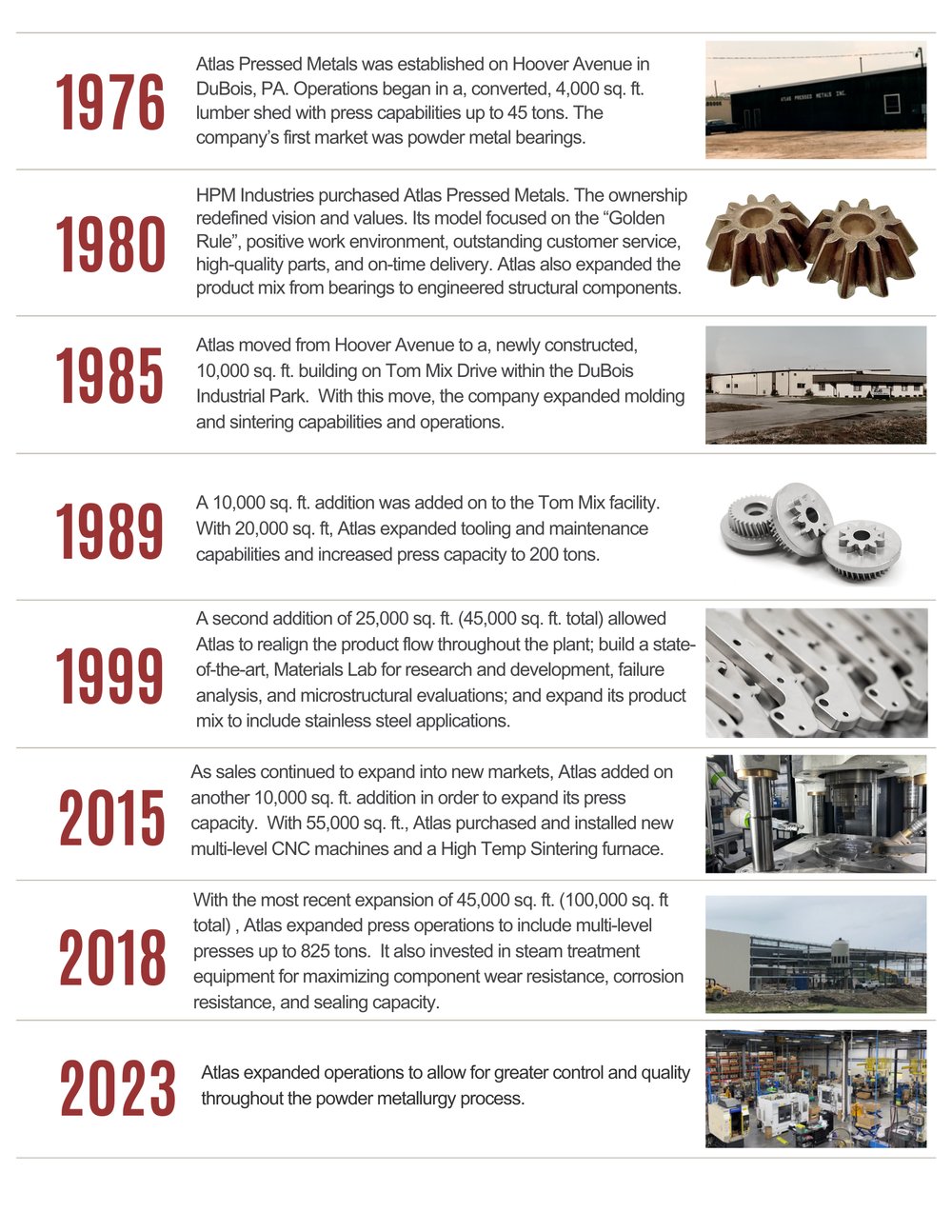
Need a Solution?
Ask Us a Question
Contact Information
Mailing Address
125 Tom Mix Dr.
P.O. Box P
DuBois, PA 15801
USA
Phone
Fax
Testimonial
"Our Engineering team works directly with Atlas Pressed Metals to achieve our company goals. Atlas is always very helpful, gives us on-time delivery and the sales reps are always willing to research to get answers for our needs.”
- Amanda S., Associate Buyer | Healthcare Industry