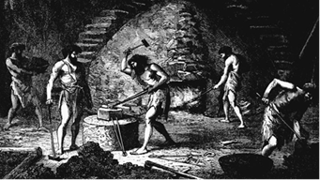
Improving on an Ancient Process, Modern Methods of Heat Treating Sintered Steel
Innovative Solution #10942
The use of Sinter Hardened Powder Metal to achieve a microstructure optimized for yield strength and cost effectiveness.
Overview
An update to an existing appliance changed the lid from stamped metal to glass, increasing the weight of the lid. As a result, the stress on the existing powder metal cam used in the hinge assembly also increased.
Challenge
The existing powder metal cam has geometric features that made it expensive to manufacture on a repeatable basis in high volumes using other processes, such as machining, welding or broaching. The key requirements of the component, a countersink into a bore and unequal hub lengths while maintaining balanced density, and keeping an eye on cost, lent itself to the powder metal process. This cam was made utilizing a common iron copper alloy which was not appropriate for the additional weight of the glass lid.
Results
Atlas Pressed Metals Engineers recommended the use of a sinter hardened material for this increased weight requirement. Typical iron copper alloy supports a yield strength of 50ksi/ (340MPa), while the sinter hardened iron chromium prealloyed powder supports a yield strength of 120ksi/ (830 MPa) in this application. Additionally, using sintered hardened material eliminates the requirement for a secondary heat treatment process, which adds cost, introduces warpage and dimensional concerns, and increased process time.
Interested in reading more about heat treatments options in the Powdered Metal process? Click here to read “Powder Metallurgical Solution for a Complex Geometry Coupler Requiring High Dimensional Stability and Microstructure Uniformity through Heat Treatment” written by Dr. Craig Stringer, Andy Wright ad Pete Imbrogno of Atlas Pressed Metals. Dr. Stringer presented this paper at ASM International Heat Treat 2021 Conference in St. Louis on September 14-16th, 2021.
ASM International is the world’s largest association of material-centric engineers and scientists. ASM is dedicated to informing, educating, and connecting the materials community to solve problems and stimulate innovation around the world.
Related Case Studies
Need a Solution?
Ask Us A Question
CONTACT INFORMATION
Mailing Address
125 Tom Mix Dr.
P.O. Box P
DuBois, PA 15801
USA
Phone
Fax
TESTIMONIALS
After finding Atlas Pressed Metal on the internet and a site visit by our CEO, we were impressed with the Atlas plant, the team and the product.
We used them for a powdered metal part for one of our customers and we have continued to use them for about 5 years. We are pleased with their expertise in making good suggestions and with their customer service.”
- John R., CNC Sales Manager | Machined Parts Manufacturer
.png?width=500&height=500&name=iso-no-background-(1).png)
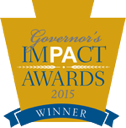
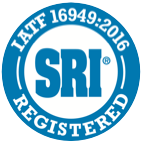